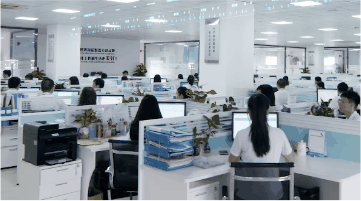
As a national high-tech enterprise, Taiqun has always regarded scientific and technological innovation, product upgrading and technological transformation as key development goals, invested heavily in scientific and technological project research and development activities, and actively carried out industry-university-research cooperation with many domestic universities and scientific research units, and achieved significant For scientific and technological achievements, more than 500 technical invention patents have been obtained. All products have passed ISO9001, ISO14000 quality and environmental system certification, and all have independent intellectual property rights. At present, the company has a technical advisory group composed of industry technical experts from mainland China, Taiwan, South Korea, Malaysia, Germany and other countries and regions, as well as a well-known R&D team of 100 people in the industry. Through scientific research activities, a team of scientific and technological personnel with both ability and political integrity has been cultivated, which has laid a solid foundation for the company's subsequent rapid development.